Negative pressure Leak Tester distribution|system pressure testing for leaks : manufacturer AHU Case Leak and Pressure Testing: With the AHU test chamber prepared for blower pressure testing, slowly introduce air into the chamber using the rig blower fan speed controller on the test rig. Advance the fan speed until the desired test pressure is achieved. Holding the fan speed steady, measure and record the orifice differential pressure. Register at Mr. Bet Mobile Casino today and take advantage .
{plog:ftitle_list}
Resultado da Liga 1 Apertura . Perú Divisão: Primeira Divisão Atual campeão: Mais vezes Campeão:
Per ANSI/ASHRAE Standard 90.1-2010, “positive pressure leakage testing is acceptable for negative pressure ductwork”. Even so, you will see specifications that may require return air or exhaust systems to be leak tested under a vacuum (negative pressure).For negative pressure testing (5b), the fan intake will be connected. With McGill AirFlow’s 4-inch Leak Detective test components, the fan comes equipped with a tapered nozzle, which can .
Working principle – general. Enclose sample in sealed an tight chamber. Apply either under- or overpressure to the chamber. Cut the inside of the chamber from vacuum / pressure supply. .This leak testing method capitalizes on the fact that a leak will allow a quantity of gas – remaining uniform through a period of time – to enter a sufficiently evacuated device (impeded gas flow, see Fig. 1.1). . the test gas which has .AHU Case Leak and Pressure Testing: With the AHU test chamber prepared for blower pressure testing, slowly introduce air into the chamber using the rig blower fan speed controller on the test rig. Advance the fan speed until the desired test pressure is achieved. Holding the fan speed steady, measure and record the orifice differential pressure.If the casing or liner top packer does not have the required integrity, there may be an additional leak path that could jeopardize the production process and even pose danger to the safety of the well. A negative pressure test, also known as the inflow test, is conducted to test the integrity of a well. While carrying out an inflow test, the .
The MPS 200 is a proven workhorse, operating on Pressure Decay for leak testing. The Electronic Pressure Regulation ensures accurate test pressure control, while the high accuracy flow sensor decreases test time and minimizes errors. The MFS 200 is available for both internal pressure test, as well as negative pressure vacuum tests.
Additional fit test series were accomplished with each mask type by inserting leak sources between each subject`s check and respirator faceseal. The leaks were used to achieve a distribution of fit test results above and below the test acceptance criterion of a fit factor of 100. Study results show that the controlled negative pressure system .
Pressure Testing: Connect one end of the orifice tube to the duct system using a short piece of single-wall flexible duct. The arrow on the calibration sticker shows direction of flow. Step 4b — Typical Negative Pressure Testing: For all standard components except the 4-inch, two options exist for performing negative pressure testing. 1.What is a Vacuum Decay Leak Test? Vacuum Decay leak testing is used on a variety of products that can only be leak tested at negative pressure. The Optima vT can be used to leak test products, typically less than one liter at a fairly low vacuum, < 0.25 atm. Testing products greater than one liter can be achieved with high flow valves.Leak Testing - TQC's beginners and fundamentals guide to helium leak testing, what is it, why use it and the benefits of helium leak testing. Please call: +44 (0)115 950 3561. . To reduce the effect of a large leaker one can; build up to the full test pressure in stages, build up to the full concentration, flush the mass spec with a gas with .
Vacuum and Pressure decay leak testing Venice, 22. March 2019 Presenter: Dr. Matthias Kahl, Head of R&D WILCO AG, CH . –LFC, P, V (different types) –pressure curve / course –steps of the differential pressure test • Method selection • Equipment in process control • Applications of differential pressure . most similar to negative .Vacuum and Pressure decay leak testing Basel, 27. February 2020 Presenter: Patrick Schlatter, WILCO AG, CH Head of Sales Europe / Key Account Manager. 2 Overview . ☺most similar to negative samples (used for method development) Determining the measuring capability of a machine: needle valve ☺adjustable orifice
Per ANSI/ASHRAE Standard 90.1-2010, “positive pressure leakage testing is acceptable for negative pressure ductwork”. Even so, you will see specifications that may require return air or exhaust systems to be leak tested under a vacuum (negative pressure). To perform a proper duct leakage test under negative pressure using an ORIFLOW duct leakage tester, perform .
The negative pressure wave approach is definitely useful in pipelines carrying liquids, but the energy of the pressure wave is spent during long flow pumping in gas pipelines. The concept of a detection and localisation method based on pressure drop in a leak free pipeline (pressure gradient method) is linear as shown in Fig. 8.Leak Testing 101: A Primer 4 Vacuum Decay Leak Testing Similar to pressure decay leak testing, vacuum decay leak testing evacuates air from the part or system under test to detect leaks. Vacuum decay leak testing is commonly used with parts that could have leaks from external sources, such as underwater sensors, pipes, or outdoor electrical .
The pressure increase leak test method can be a good alternative to trace gas methods, given the ability to test parts at very high pressures (up to 1,000 bar), with very short cycle times. . This measuring chamber is not directly pressurized with positive or negative pressure but is dosed via a previously evacuated or filled pre-volume. The .Dry air leakage rate measured at 1 atm differential pressure across an orifice leak (i.e., leak inlet pressure of 1 atm versus outlet pressure of approximately 1 Torr) at 25 . The theoretical correlations of orifice sizes to air leakage rates were provided by Lenox Laser, Glen Arm, MD. Leakage rates are approximation ranges.
This article explores the negative pressure test in drilling, explaining its importance as a safety protocol and detailing the steps involved. . Any drop in pressure indicates a potential leak or defect in the system. .Air leak testing is a common method used for leak testing. It is a flexible test method that can be used to leak test a wide variety of parts and applications. Under the umbrella of air leak testing are several specific methods. In this ebook, we’ll cover the following types of air leak testing: > Pressure Change Method A
vacuum leak testing system
Causes of Negative Pressure. Negative pressure in pipe flow can arise from a variety of circumstances. Firstly, a sudden change in flow velocity can lead to negative pressure. This abrupt alteration could be due to the closing or opening of valves, starting or stopping a pump, or changes in the pipe geometry. The negative pressure wave (NPW) based technique analyses the detection time of leak-induced acoustic waves by sensors in proximity, and Pressure Point Analysis (PPA) based methods detect the leak based on the decrease in pressure values owing to leaks [58], [61]. These methods are more suitable for straight pipeline and are likely to fail to .The 6D Laskin-Nozzle aerosol generator is a small, light yet rugged portable, self-contained generator. It is ideal for testing a wide variety of filter systems with airflows up to 2,000 cfm by generating a polydispersed, submicron aerosol. Applications include workstations, negative pressure filtration units, biological safety cabinets, ceiling modules and more. It can also be [.]Negative pressure wave is a popular method to detect the occurrence and location of leak incidents in oil/gas pipeline. Three core technical challenges and related algorithm are discussed in this paper. The first is data quality. The balance between noise level and locating precision is discussed in filter design. The second one is dynamic slope in anomaly detection, whence a bi .
Examples might be AWWA standards for water transmission and distribution system piping. Leak-Testing Methods. There are many different methods for pressure and leak testing in the field. Seven of these are.. . Vacuum testing, which uses negative pressure to check for the existence of a leak; . Leak Test - A pressure or vacuum test to .TEST EQUIPMENT – NITROGEN ENRICHED AIR DISTRIBUTION SYSTEM NEGATIVE PRESSURE LEAK CHECK: 7: Aviapool (Aviation Tool Pooling LLC) is a global company providing around the clock assistance for the planning, supply, and sourcing of tooling equipment to the commercial aviation marketplace. Understanding the negative pressure test on a drilling rig is crucial for maintaining control and ensuring safety. This article explains the importance of this test and provides a step-by-step procedure for conducting it effectively. . If the pressure drops, it may indicate a leak in the chamber or a malfunctioning component that needs . Transformer Testing. The purpose of this article is to provide a list of the standard battery of tests performed on reconditioned and new transformers, while also providing an introductory explanation of the purpose and scope of the most common routine factory and diagnostic field tests.Factory testing is performed according to IEEE C57.12.00 and IEEE .
Pressure decay is one of the most widely used methods of leak testing in manufacturing and is ideal for a sealed component with an access port. In this test, a product is attached to a leak tester and filled with air. Once pressurized, the air source is valved off and the pressure is allowed to settle.The Pressure Decay test, also known as gauge decay, absolute pressure, leak drop or delta pressure leak test. This test method measures the drop in pressure on a gauge (transducer) during the leak test. Pressure decay leak testing is used to test products for leaks by trapping pressure inside a product and then measuring pressure loss.
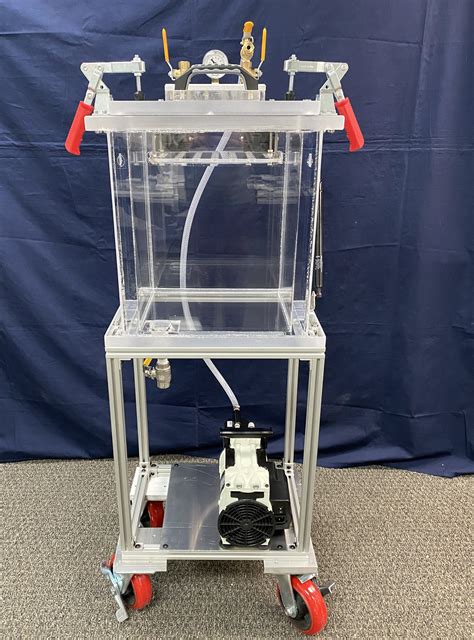
s13 sr20det compression test guide
s13 sr20det compression test hot or cold

WEBCarlos Pinhu é um renomado tatuador com mais de 20 anos de experiência e é frequentemente colocado como um dos 10 melhores tatuadores de São Paulo.. Além de sua especialidade em tatuagens tribais das tribos marquesa, samoa, maori e indígenas americanos e brasileiros, ele oferece uma ampla variedade de outros estilos de .
Negative pressure Leak Tester distribution|system pressure testing for leaks